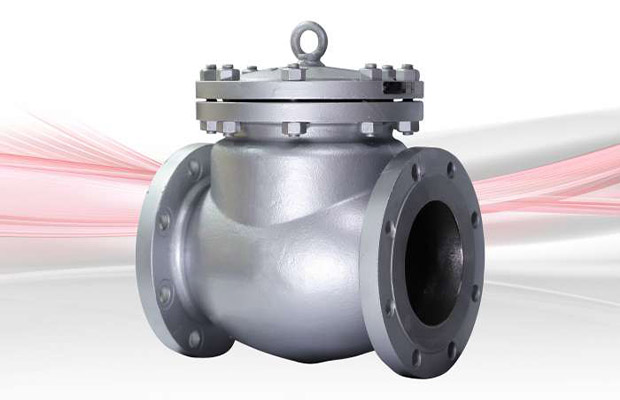
What is a check valve? A check valve, also known as a one-way valve, is a component that only permits one direction of fluid flow. A check valve’s main objective is to keep backflow from occurring in the system. Check valves are an affordable, simple, and efficient solution to a potential problem.
Common check valve problems include water hammer, vibration, noise, reverse flow, and so on.
Here is the internet’s most comprehensive guide to check valves. Keep reading.
Table of Contents
What Is Check Valves?
Designed to allow fluids and gases to flow in one direction while preventing reverse flow, a check valve is an automatic safety device. Fluids enter the valve at the inlet under pressure, forcing the disc of the valve seat, and exit the valve through the outlet.
As long as the pressure is kept high enough to keep the disc open, the flow remains constant. The disc automatically returns to its seat to stop the flow once there is a pressure drop.
The cracking pressure, which varies from 3 psi to 350 psi depending on the size, function, and purpose of the check valve, is what causes the valve to open.
Check valves to make sure that liquids or gases are flowing in the right direction and seal tightly to stop leaks. Check valves prevent serious harm to pumps and compressors by regulating the flow of liquids.
Check valves have different names depending on how and for what they are used. They are also known as clack, non-return (NRV), reflux, retention, and one-way valves. Despite the fact that their design and operation are straightforward, they play a crucial role in the safety of pumps, piping systems, and fluid flow.
The swing valve, the most typical type of check valve, is depicted in the picture below. The disc is completely out of the way during fluid flow because it is a full port design. The disc is unlocked by the directional flow. The disc stays open as the flow goes on. As the flow decreases or stops, the disk is pulled closed by gravity.
Reverse flow, which can harm pumps and other mechanisms, is largely avoided by check valves. A potential water hammer occurs when a check valve closes and fluid in a system slams against the closed check valve. This feature of a check valve’s operation necessitates that they are strong, resilient, and constructed of premium materials.
The noise produced by check valves must be muted because they can be noisy. Diverse types of controls are added to that end. The structure of the valve is built with springs, levers, or weights to control surges and stop the valve from closing abruptly.
Read More: What Is An EGR Valve?
How Do Check Valves Work?
Cracking Pressure
In order to open a check valve and allow media to pass through it, there must be a minimum upstream pressure (pressure difference between the inlet and outlet). It is known as the check valve’s “cracking pressure” to refer to the lowest upstream pressure at which the valve opens.’ Make sure the system’s pressure can generate the cracking pressure of the selected check valve(s) because the specific cracking pressure varies depending on the valve design and size.
Closing
The check valve will close if the upstream pressure drops below the cracking pressure or if there is back pressure (flow attempting to move from the outlet to the inlet). In order to close the check valve, it is common for check valves to have a gate, ball, diaphragm, or disc. The closing process may be aided by gravity or a spring. The valve closes by gravity, a spring, and/or by utilizing backpressure as soon as the inlet pressure drops below the cracking pressure or there is back pressure.
Normally Open And Normally Closed Check Valves
A normally open check valve allows the medium to flow freely but shuts off the flow in the event of backflow. A normally closed check valve prevents media from passing through it until the cracking pressure reaches a certain level, at which point the valve opens.
Installation Orientation
Knowing the proper installation orientation is essential because one-way valves only allow flow in one direction. Usually, the flow direction is indicated by an arrow on the valve housing. If there isn’t an arrow, make sure the valve is installed in the proper flow direction by looking at it. The system won’t be able to move media if the valve is installed backward, and the resulting pressure build-up could result in damage.
Different Types Of Check Valve
Depending on their design, check valves perform in various ways. A spring-loaded in-line check valve is the most typical type of check valve, but we’ll talk about several others below.
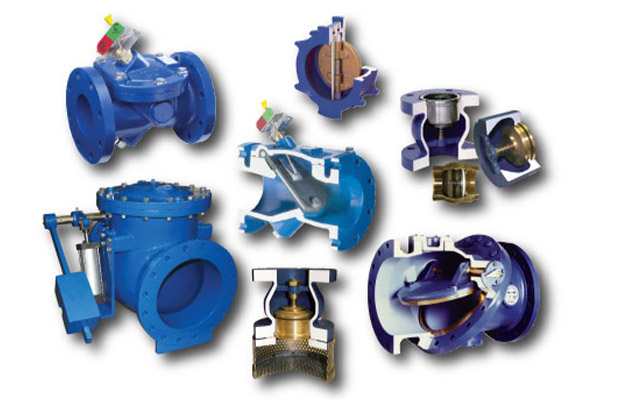
Spring-loaded In-line Check Valve
Common, understandable, and straightforward in their design are in-line spring-loaded check valves. A spring-loaded in-line check valve is shown in Figure 2 in both the open and closed positions. The flow direction is denoted by the arrows. It should be possible for the flow to overcome the cracking pressure and the spring force when it enters the valve’s input port. The disc is forced by the pressure, which also causes the orifice to open and permit flow through the valve. The back pressure and spring push the disc against the orifice and seal the valve shut when the input pressure is no longer high enough or there is sufficient back pressure. A quick reaction time is possible for closing thanks to the spring and the disc’s short travel distance. This valve’s design also prevents pressure spikes in the line, which reduces water hammer.
Typical names for spring-loaded in-line check valves include “nozzle check valves,” “poppet check valves,” “axial check valves,” “excess flow check valves,” “silent” or “quiet” check valves, and “antiwater hammer check valves.”‘ They can be mounted either vertically or horizontally. However, because they are part of the system, they must be completely taken off the line in order to be examined and/or maintained. Two spring-loaded plates are mounted on a central pin in a dual plate check valve. This construction effectively prevents slamming and water hammering.
Spring-loaded Y-check Valve
Similar to in-line spring-loaded check valves, spring-loaded y-check valves function similarly. The movable disc and spring are positioned differently because they are at an angle. The “Y” shape that results from this gives the valve its name. It functions in the same way as an in-line valve, but because the moveable parts are angled, they can be inspected and maintained even when the valve is connected to the system. These valves are bigger and take up more space inside the system.
Butterfly Or Wafer Check Valves
The terms wafer check valve and butterfly check valve are frequently used interchangeably. They are made up of a butterfly- or wafer-shaped disc mounted on a hinge and a spring. Figure 9 illustrates what happens when inlet pressure surpasses cracking pressure and the two sides open. The hinge’s spring will close the disc and seal it when the inlet pressure drops or there is backflow, whichever occurs first. A straight media flow is permitted by this valve type with little obstruction. Wafer swing check valves have a modern appearance and can be installed in small flange spaces.
Diaphragm Check Valve
When the inlet pressure rises, a rubber diaphragm in a diaphragm check valve flexes open. Figure 5 (left) depicts a normally open diaphragm check valve with “minimal” inlet pressure that permits media to pass through. The diaphragm will flex open, allowing more flow, as shown in Figure 5 (middle), as the inlet pressure rises. As shown in Figure 5 (right), the diaphragm will be forced against the opening and seal it to prevent any backflow if backpressure occurs (or if it is a normally closed diaphragm check valve). Low-pressure or vacuum applications are perfect for diaphragm check valves.
Lift Check Valve
A guided disc that lifts off the valve seat to permit media flow is the main component of a lift check valve. To overcome the resistance of gravity and/or springs, it needs a cracking pressure. The guide maintains the disc in a vertical position so that it can be reseated with the right alignment and seal.
As shown in Figure 6, lift check valves most frequently require the media to turn 90 degrees. If there isn’t a spring to help the disc close, mounting orientation must be taken into account to make sure that it does so naturally.
Ball Check Valve
A free-floating or spring-loaded ball that rests on the sealing seat is used by a ball check valve to close the orifice. The sealing seat is typically conically tapered to help the ball enter the seat and form a positive seal, which prevents reverse flow. The ball is knocked out of its seat and allows flow when the fluid pressure on the inlet side is higher than the cracking pressure. The ball will close with the back pressure or through the spring if the inlet pressure does not exceed the cracking pressure or there is back pressure, thereby effectively closing the orifice. True union ball check valves make it simple to remove and replace balls, negating the need to purchase a new valve. For more details, read our article on ball check valves.
Swing Check Valve
The terms “tilting-disc” or “flapper” check valves are used to describe swing check valves. With an inlet pressure, a disc on a hinge (also known as a trunnion) swings open. As inlet pressure drops or if backflow occurs, the disc swings shut. Consideration should be given to mounting orientation if there isn’t a spring to help the disc close if it isn’t, in order to ensure that it does so naturally. A dual disk or double door check valve has a central disk that is divided into two semicircular doors. The doors are hinged on a central pivot point and operate independently. A swing check valve is demonstrated in Figure 7. If you’d like more details, read our article on swing check valves.
Stop Check Valve
A lift check valve with a manual override feature or a spring-loaded y-check valve is common examples of stop check valves. As a result, the valve can operate as a typical check valve and stop backflow. The valve can be kept in an open or closed position using an external mechanism. Consequently, a stop check valve can serve as two valves in one: a flow regulating valve and a backflow preventing valve. In power plants, steam generators, turbine cooling, and safety systems are frequently used in the circulation of boilers.
Duckbill Check Valve
As shown in Figure 10, duckbill valves permit flow through a flexible tube with a naturally flattened end. The valve’s name comes from its flattened shape, which resembles a duck beak. The duckbill’s flattened end is opened by the flow, allowing media to pass. The duckbill end returns to its flattened state when pressure is released from the inlet side, cutting off the flow.
Foot Valve
On the inlet side of a foot valve, there is a check valve and a strainer. The strainer keeps debris out of the check valve that could obstruct it or harm downstream components. Since the input of this valve lacks a connection point, it is placed at the end of a section of piping. Foot valves frequently have in-line ball or spring-assisted check valves. In any application where the suction line is located below the pump, such as a water well or fuel tank, they are typically installed at the end of the pump suction line. Pumps can be kept primed with their help, as can be done to keep debris out of the line and stop liquid from siphoning back. Figure 11 depicts a foot valve in action.
Dual Plate Check Valve
A central pin supports two spring-loaded plates that make up a dual plate check valve. Water hammer and slamming are effectively avoided by this design.
When Should You Use Check Valves?
Check valves are useful to prevent backflow from a water source from contaminating treated or potable water sources or when there is a risk that backpressure from the distribution system will harm a pump.
They are especially beneficial in applications where backflow would be problematic. The media upstream is also contaminated if the backflow is tainted. As a result, these valves are widely used in drinking water distribution systems and treatment facilities.
Check valves are also used in centrifugal pumps because they don’t self-prime, making them crucial for maintaining water pressure in the pipelines.
Where To Put Check Valve?
To guard a pump against backflow, check valves are frequently installed on the outlet side of the pump. There may be requirements for the valve’s location in relation to other equipment, depending on the application. As a result, it is advised to speak with the valve manufacturer, an engineer, or a consultant to ensure proper positioning for the valve’s best use.
Uses Of Check Valves
Since the self-sealing valve was created at the start of the 20th century, it has been the solution to backflow issues in a variety of industries. A check valve is a component of any system used by industry to transport goods through pipes.
Check valves are economical appliances that reduce waste and safeguard machinery. It’s important to avoid losing fluids that move through a piping system because of careless handling. When pressure or flow decreases, check valves automatically stop the flow of liquid by preventing backflow and keeping the fluid inside.
Check Valve Uses
Pumps
One of their more popular applications is as check valves in pumps.
- Single pump system: The check valve regulates the flow from a suction tank and prevents it from reversing when the pump stops.
- A check valve in a parallel pump system keeps the duty pump from pumping into the standby pump in a parallel pump system.
- Series pump system: When pumping materials in a pipeline over great distances, a series of pumps is used. The check valve opens to stop losses in the event that any of the pumps in the series fails.
- In gas applications, spring-loaded check valves are used for low-pressure situations as a form of pressure relief. The check valve securely releases the gas if the system pressure exceeds the cracking pressure.
- Foot valve: When the pump is turned off, the foot valve keeps debris from entering the well and keeps water from recirculating.
Aviation Hydraulic Systems
The hydraulics of the landing gear actuator system utilizes orifice check valves. Fluid flows to lift the gear when it is lifted. By regulating the flow out of the actuator when the gear is lowered, the check valve prevents the gear from dropping. Check valves are used in other hydraulic, fuel, and pneumatic systems on aircraft in addition to the landing gear.
Pharmaceutical
Check valves are needed for the flow of fluids in the pharmaceutical industry. For fluid flow efficiency, production efficiency, and product quality, check valve control pressure. This procedure can only be carried out using sanitary check valves. They need to close quietly with a tight shut-off and be simple to clean without the need for disassembly.
Irrigation Systems
In order to prevent backflow, or siphonage, of irrigation water back to the source, check valves are placed close to the source of the system in irrigation systems.
Fuel Pump
Before the development of the electronic injection system, check valves were used in automobile construction. Older automobile fuel pumps have check valves at the inlet and outlet that are intended to force fuel to flow in the desired direction. Fuel pressure decreases as a result of a bad check valve.
Check Valves For The Water Supply
Only the supply line and a fixture, or a drain and the sewer, should move water in a house. To stop cross-connection or backflow, check valves are installed in homes. They are available in a number of variations, such as ball and swing check valves. The diagram of a home’s hot water system can be seen below, along with domestic check valves.
Heating Boiler
When the thermostat is not requesting heat, check valves on heating boilers to stop the circulation of hot water. They prevent water from returning to the boiler, preventing the pressure from rising too high. A check valve prevents boiler water from entering the domestic supply in a boiler used for home heating, preventing it from being used for drinking, bathing, or cooking.
Liquid Fuel
Jet fuels, hydraulic oil, synthetic oil, and even air can all be used with liquid fuel check valves. They are made to function steadily from the valve’s crack to its maximum flow. To ensure balance and stability and to maintain a specific delta pressure in the valve, an inverted spool with a built-in pressure sensor is employed. The valve can open evenly due to the overall design.
Pros And Cons Of Check Valves
Check valves’ ability to function without needing to be monitored or controlled is one of their main advantages. Their fundamental structure enables them to be inserted into a pipe’s flow and control the flow without being managed.
Despite all of their advantages, check valves have disadvantages just like any other kind of mechanism.
Pros Of Check Valves
- Prevent backflow
- Able to endure high and low-pressure conditions
- Perform as a backup and safety system
- Able to be used horizontally and vertically
- Self-actuated
- Few moving parts
- Smaller footprint
- Able to cope with variable flow conditions
- Do not require power to operate
- Fast acting.
- Protect pumps and compressors from damage caused by backflow
- Reduce downtime and loss of production
- Prevent water hammer
- Reduce sudden valve failure
- Lower maintenance costs
Cons Of Check Valves
- Do not operate in pulsating systems
- Water hammer
- Reverse flow problems
- The closing element can slam closed causing damage and wear
- Operate in a completely enclosed system
- Impossible to check if they are open or closed
- Internal parts cannot be checked
- In the open position, disks may become stuck.
- Noise from slamming discs
Some Common Problems With Check Valves
Oversizing
Chattering in some check valve systems is brought on by frequent valve opening and closing. The check valve’s oversizing is to blame for this. A check valve needs to be sized to fit the application before installation. In order to avoid repeated opening and closing, fluttering, and failure of the check valve, the disc must be stable in the open position and create a complete seal when closed.
Water Hammer
When a gas or liquid flow suddenly stops and a valve suddenly closes, there is a pressure surge that results, causing noise and vibrations known as “water hammer.” Water hammers can harm the system and require expensive repairs.
By having check valves that close more quickly, pressure surges and shock waves can be stopped, preventing water hammer. Check valves with silent operation are one option.
Reverse Flow
In addition to being expensive, reverse flow can harm pumps by making them spin counterclockwise. Check valves that fit snugly and close quickly can solve this issue. The ability of spring-assisted check valves to react quickly and prevent reverse flow is one of their advantages.
Installation
Future issues may result from improper check valve assembly and installation. Choosing the appropriate check valve for the application is the first step. Since installing a check valve too close to a pump can result in turbidity and possible check valve damage, flow capacity, positioning, and orientation are important considerations.
To avoid turbulence and the disc rattling against the seat, check valves should be installed upstream of circulators, elbows, tees, and strainers by several straight pipe diameters.
Can A Check Valve Prevent Backflow?
An example of a backflow preventer is a check valve, but the main distinction between the two is how they are used.
When there is a high risk, a backflow preventer is used to completely safeguard the potable water. Where the domestic water piping of a private building meets the water supply from the city, backflow preventers are frequently installed. Additionally, they are frequently used in situations where potable water is connected to non-potable water.
The use of a check valve, on the other hand, prevents the flow of water backward in low-risk circumstances. The fail-safe components in a backflow preventer are more numerous than those in a check valve.
The Bottom Line
A check valve is a unidirectional valve that allows fluid to flow in one direction while blocking all flow in the other. An important function of a check valve in a system is to stop backflow, which has the potential to contaminate media upstream or damage equipment.
After reading, please leave a comment if you have any additional queries that weren’t addressed in this post.